Khái niệm chungChọn cơ chế cắt là khẳng định chiều sâu cắt, chu kỳ chạy dao, lượng chạy dao, tốc độ cắt cùng công suất quan trọng trong điều kiện gia công nhất định.
Bạn đang xem: Chế độ cắt khi tiện
Chế độ cắt hợp lý là chế độ cắt tốn ít thời hạn nhất để sản xuất sản phẩm vì chưng đó ngân sách chi tiêu của nó phải chăng nhất. Nếu tìm đúng kết cấu dao, thông số hình học phần cắt, vật liệu, phương pháp mài sắc và mài bóng cũng giống như xác định đúng đắn cách gá đặt, kẹp chặt dao với phôi, điều chỉnh máy tốt, trang bị công nghệ có kết cấu hợp lí sẽ tạo đk để chọn cơ chế hợp lý và gồm lợi.
Chế độ cắt chịu sự tác động của một loạt các nhân tố như nguyên tố hoá học của đồ vật liệu, phương thức sản xuất và tối ưu nhiệt, kết cấu tế vi, độ phệ của hạt và mạng lưới tinh thể. Các yếu tố trên nhiều khi tác động một cách cứu giúp nhau đến cơ chế cắt và không thể reviews độc lập, cô đơn nhau. Cơ chế cắt còn phụ thuộc vào phương pháp gia công, loại vật liệu dao, thông số hình học điều khoản cắt, đk gá, kẹp chặt cụ thể vì vậy cơ chế cắt hết sức phức tạp, thường xuyên được chọn theo kinh nghiệm tay nghề và sử dụng những công thức thực nghiệm nhằm tính toán chính sách cắt.
Trong nghành chế tạo máy có không ít loại đồ vật liệu không giống nhau được sử dụng, trong và một loại lại sở hữu thành phần, cấu trúc, độ cứng rất khác nhau, vì vậy để mang ra một công thức ví dụ để tính chính sách cắt mang lại từng nhiều loại vật liệu, điều kiện gia công ví dụ là ko thể tiến hành được. Bởi vì vậy, chính sách cắt được tính cho một trong những vật liệu chuẩn ứng với cùng 1 số điều kiện nhất định làm sao đó, còn các vật liệu khác được tính nhờ các hệ số tối ưu thực nghiệm.
Khi sử dụng cơ chế cắt trên bản vẽ chế tạo cần yêu cầu vạch rõ những yêu ước về độ đúng mực kích thước, hình dáng, độ bóng mặt phẳng sau khi gia công, đặc trưng vật liệu thành phầm như nhãn hiệu thép, tâm lý cơ tính và trạng thái lớp bề mặt phôi.
Các thông số kỹ thuật cắt
1. Chiều sâu cắt t(mm): là khoảng cách giữa các mặt phẳng đang và đã tối ưu đo theo hướng vuông góc cùng với mặt đã gia công.
2. Lượng chạy dao s (mm ):là khoảng tầm cách di chuyển của dao trên vòng quay của phôi (hành trình làm cho việc) hay là khoảng dịch chuyển của phôi sau một vòng của dao (hành trình có tác dụng việc).Thường gồm lượng chạy dao dọc, ngang, ở ngang,thẳng đứng nghiêng hoặc hay những lượng chạy dao hòn.
3. Chiều rộng lớn của phôi b (mm): là khoảng cách giữa các mặt phẳng đang với đã gia công đo theo khía cạnh cắt.
4. Chiều dày phôi a (mm): là khoảng cách giữa nhị vị trí tiếp tục của mặt phẳng cắt sau một vòng quay của phôi xuất xắc sau một lần chạy dao, đo theo phương vuông góc cùng với chiều rộng phôi.
5. Diện tích phôi f (mm2): là chiều sâu cắt t với lượng chạy dao s hoặc chiều rộng lớn phôi b cùng với chiều dày a (f = ts = b a ).
6. Tốc độ cắt V (m/ph): là đoạn đường dịch chuyển của lưỡi cắt so với mặt đang tối ưu trong một đơn vị thời gian. Tốc 1 đơn vi thòi gian. Tốc độ cắt lúc mài tấn công bóng và những nguyên công giống như tính ra m/s.
Trình từ bỏ tra cơ chế cắt khi tiện (Các phương pháp gia công khác cũng rất được tra theo trình trường đoản cú tương tự)
1. Chiều sâu cắt t, mm: Để giảm bớt thời gian gia công, thời gian phụ nên chọn lựa số lần chạy dao là không nhiều nhất. Tối ưu thô: t lấy bằng lượng dư.Gia công tinh: với bề mặt có độ nhẵn bóng tốt hơn cung cấp 5 thì t = 0,5 — 2 mm, với cấp cho 6, 7 thì t = 0,1 — 0,4 mm Chú ý: Khi giảm đứt và tạo thành rãnh, tiện thể định hình, t = chiều rộng lớn của lưỡi cắt.
2. Tra lượng chạy dao s, mm/vg: khi sử dụng lượng chạy dao nên chú ý những nguyên tố sau đây: Yêu cầu độ bóng bề mặt, độ chống rung đụng của hệ thống máy-dao-chi tiết: độ bền vững của dao, sản phẩm công nghệ gia công bảo vệ công suất. Giá trị lượng chạy dao tra ở các bảng (14-12)
1. Lượng chạy dao luôn tiện thô mặt quanh đó và tiện cắt đứt bởi dao thép gió với dao kim loại tổng hợp cứng
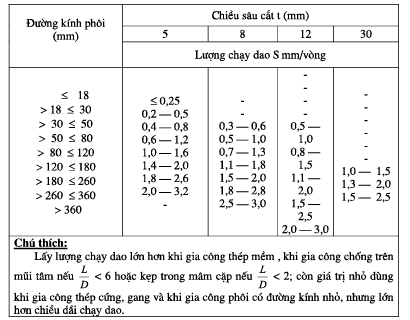
2. Lượng chạy dao khi tiện quanh đó thép tôi bằng dao hợp kim cứng
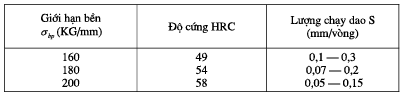
3. Lượng chạy dao khi tiện tục tằn trên sản phẩm công nghệ tiện
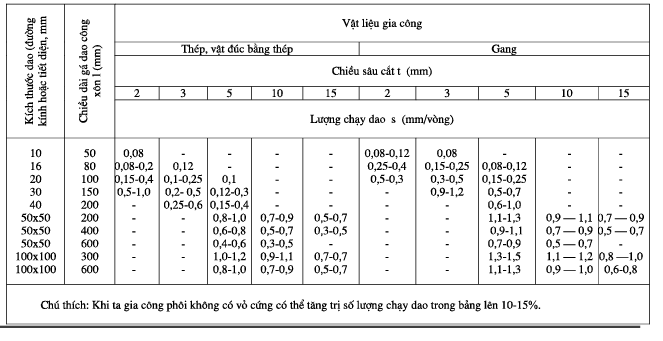
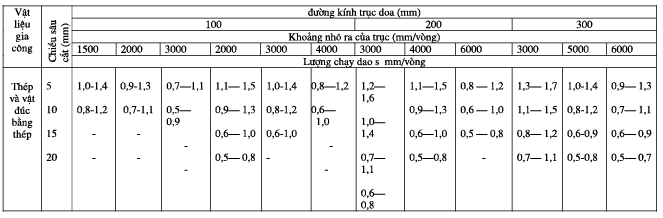
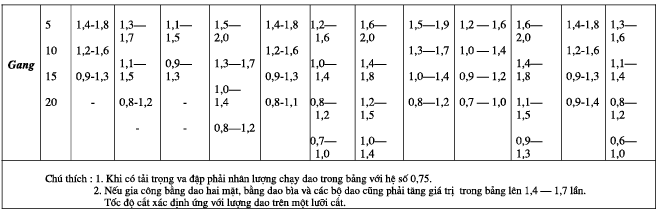
5. Lượng chạy dao nên dùng làm tiện thép cùng gang bởi dao tiện gồm lưỡi giảm phụ.
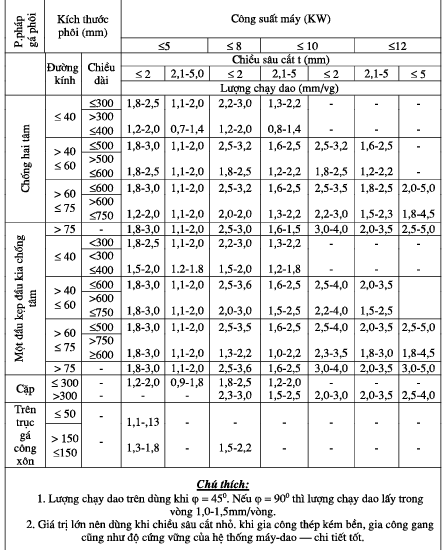
6. Lượng chạy dao tiện xung quanh và bào thép tất cả ơb = 90 4- 70 KG/mm2 bằng dao thép gió và dao hợp kim cứng
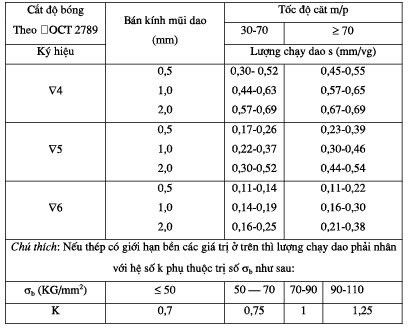
7. Lượng chạy dao một thể ngoài hợp kim đồng đúc bằng dao thép gió và kim loại tổng hợp cứng.
điều khoản cắt gọt sắt kẽm kim loại Dụng núm kim cương phương pháp đo chế độ cầm tay luật dùng năng lượng điện Phụ kiện tối ưu Vòng bi sản phẩm đá mài những loại khác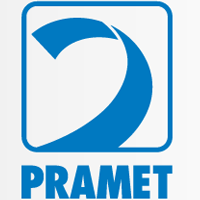

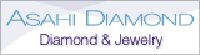
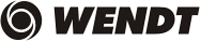
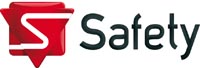
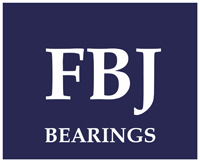
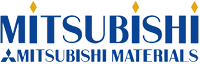
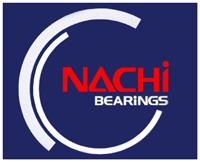
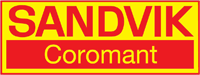
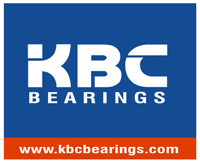
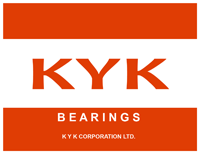
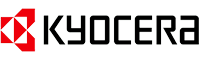
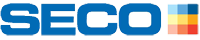
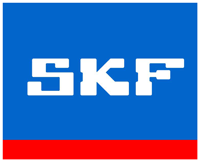
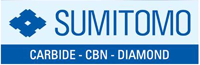
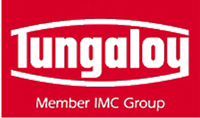
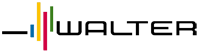


![]() | Hôm nay | 2643 |
![]() | Hôm qua | 3302 |
![]() ![]() ![]() ![]() ![]() | Tất cả | 5150400 |
Chế độ giảm khi tiện
Chế độ cắt khi tiện :Chiều sâu cắt t (mm) : là lớp kim lọai đượcTiện đi vào một đường gửi dao chiều sâu giảm được đo theo phương vuông góc với bề mặt gia công.
D - d
t = ------------- (mm)
2
Trong kia : D : là đường kính đang gia công (mm)
d: là đường kính đã gia công (mm)
Khi tiện đường kính lỗ chiều sâu giảm là nửa hiệu của đường kính lỗ sau khi gia công và 2 lần bán kính lỗ trước lúc gia công.
Khi tiện mặt đầu chiều sâu cắt là kích cỡ của lớp kim lọai ngắn hơn theo phương vuông góc với phương diện đầu.
Xem thêm: Bảng xếp hạng những con vật thông minh nhất trên trái đất, top 10 loài vật thông minh nhất thế giới
Khi tiện giảm đứt chiều sâu cắt là chiều rộng của rãnh được cắt.

2.Lllượng chạy dao s (mm/vòng) : là quãng đường dịch rời của đỉnh dao theo phương chạy dao trong một vòng xoay của phôi.
Tốc độ giảm V (m/phút) :

Tốc độ cắt là quãng lối đi được của một điểm xa nhấttrên mặt phẳng cắt kha khá so cùng với đỉnh dao trong một đơn vị chức năng thời gian,thì được gọi là tốc độ.

Trong hình trên ta thấy 2 lần bán kính D của phôi càng lớnthì tốc độ cắt V càng mập với cùng một số vòng con quay n của trục chính(của đưa ra tiết).
Khi biết tốc độ cắt V và đường kính của cụ thể D có thể tính được số vòng quay n của phôi (của trục chính) và điều chỉnh hộptốc độ để sở hữu số vòng quay
1000V
n = -------------
π D
Phương pháp mài dao tiện :
Trong quy trình cắt gọt dao thường bị mài mòn với dẫn đếnthời điểm nào đó sự mài mòn của dao đạt tới độ mài mòn có thể chấp nhận được thì nên mài lại dao.
Mài sắc đẹp dao tiện thể được áp dụng mài trên máy mài 2 đá

Trình từ bỏ mài như sau:
1.Mài khía cạnh sau chính
2.Kiểm tra góc sau chính sau khi mài
3.Mài khía cạnh sau phụ
4.Kiểm tra góc sau phụ bằng dưỡng mài dao
5.Mài khía cạnh trước
6.Kiểm tra góc trước khi mài
7.Mài nửa đường kính mũi dao
Rà tinh.
Những điều cần chú ý trong lúc mài dao :
1.Tư thế nạm dao phải chủ yếu xác, những ngón tay phải ổn định không rung.
2.Khi mài bằng chất liệu thép gió phải thường xuyên làm mát để tránh đến dao khỏi bị cháy.
3.Khi mài bên trên đá không mài bên cạnh hông của đá.
4.Khi mài, mang lại dao cầm tay hết bề ngang của đá, tránh việc mài một nơi trên đá mài.
5.Khi mài không nên dùng lực quá lớn để kiêng bị trượt tay đập vào đá mài.
6.Khi mài phải đứng về một mặt của đá để tránh những hạt mài bắn vào mặt, tốt nhất là treo kiếng bảo hộ.
7.Khi bề ngòai của đá ko tròn đều, bị đảo thì không nên mài tiếp mà đề xuất dùng cây sửa đá nhằm sửa mang lại tròn đều.
Khi đá mài quay chưa ổn định thì ko được chuyển dao vào mài.
Cách gá dao :
Gá đính dao một cách đúng chuẩn có ảnh hưởng lớn quá trình cắt gọt với độbóng mặt phẳng chi máu gia công, một dao tiện có các góc hòa hợp lý, tuy thế nếu gá lắp không đúng thì những góc của dao đã bị thay đổi

Khi tiện thể trụ ngòai :
Khi gá dao ngang trung tâm thì các góc độ của dao không cố gắng đổi.
Chiều dài nhô thoát khỏi ổ dao không được vượt thừa 1,5h (h là độ cao của thân dao), trường hợp gá dao cùng với chiều nhiều năm nhô ra to hơn 1,5h thì trong quá trình cắt gọt dưới chức năng của lực cắt p. Sẽ tạo cho dao bị uốn nắn hay tất cả thểgẫy dao, khi dao bị uốn nắn mũi dao sẽ ở đoạn thấp chổ chính giữa dẫn mang lại kích thướcvà độ bóng mặt phẳng chi tiết sẽ ráng đổi.
Khi gá dao cao hơn nữa tâm lắp thêm một khỏang, phương diện phẳng giảm gọt cùng mặt phẳng đáythay thay đổi dẫn mang đến góc sau và góc trước của dao chuyển đổi nghĩa là góc sau sút , góc trước tăng. Lúc gá cao chổ chính giữa góc trước tăng góc sau giảm mặtsau chủ yếu của dao tựa vào cụ thể gia công tạo nênrung hễ trong quátrình giảm – độ bóng sẽ không còn cao.
Khi gá dao phải chăng hơn tâm máy vị mặt phẳng giảm và khía cạnh phẳng đáy biến hóa dẫntới góc sau tăng với góc trước giảm bởi góc trước giảm đk thóatphoi khó khăn dẫn mang lại lực cắt tăng